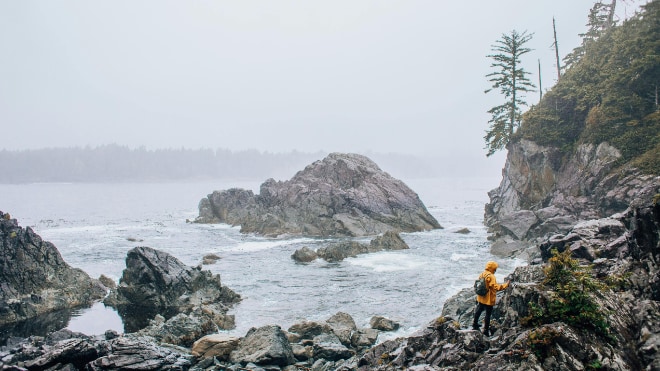
The Corrective and Preventive Action (CAPA) process is a central component of Quality Management Systems (QMS) and is a mandatory requirement for ISO 13485, MDSAP, Regulation MDR (EU) 2017/745, and the US FDA. It is a systematic approach used to identify, address, and prevent the recurrence of problems.
A CAPA is a structured process used to identify, resolve, and prevent the recurrence of issues within a system or product. It is essential for ensuring quality, compliance, and continuous improvement in various industries such as healthcare, manufacturing, and pharmaceuticals in the UK. The CAPA process is typically broken down into three main phases: Identify Problems, where issues are first recognised and thoroughly assessed; Address Problems, where corrective actions are formulated and implemented to fix the immediate problems; and Prevent Recurrence, where long-term solutions and preventive measures are established to ensure that the issue does not happen again, ultimately enhancing the reliability and quality of operations.
Key terms
Here are some key terms that all medical device professionals should acquaint themselves with:
Nonconformity = A deviation from a specification, standard, or an expectation
Nonconformity is the recognition of an issue that deviates from the expected outcome or requirement. These typically appear at the beginning of the process, during identification and investigation stages.
CAPA Trigger = A predefined condition that leads to a corrective or preventative measure
CAPA triggers can arise from various sources, both internal and external, and typically highlight areas where a product, process, or system does not meet specified standards or expectations. Examples of CAPA triggers include: customer complaints, audit findings, and adverse events or near misses.
Root Cause Analysis (RCA) = A method to identify the cause of a problem
The goal of RCA is not just to address the immediate symptoms of a problem, but to discover and resolve the root cause(s) to prevent recurrence. It’s a critical component of the CAPA process, especially in regulated industries like manufacturing, healthcare, and quality control. Tools such as the 5 Whys, Fishbone Diagram, and Failure Mode and Effects Analysis (FMEA) can be used to facilitate RCA.
Root Cause = The main reason why a problem has arisen/occurred
In any quality management or problem-solving process, identifying the root cause is critical because it allows an organisation to focus its efforts on eliminating the source of the problem, rather than just addressing its symptoms.
Field Corrective Action (FCA) = Actions to address issues identified after distribution
FCAs are typically initiated after a product defect, safety concern, or performance failure has been identified in the field, often through customer complaints, product recalls, or post-market surveillance data. They form an important part of the product lifecycle and help in protecting both the end users and the manufacturer’s reputation.
Supplier Corrective Action Request (SCAR) = A request to a supplier to address the problem
The SCAR process is used to communicate nonconformities, initiate corrective actions, and ensure that suppliers address the underlying issues causing defects or quality problems. It’s an essential tool in quality management systems. The purpose of SCAR is to improve supplier performance and prevent recurrence of issues that may affect the quality and safety of the end product.
CAPA Plan = A documented plan for actions to address a specific issue
It begins with identifying a problem, conducting a root cause analysis, and implementing corrective actions to resolve the issue. Preventive actions are then put in place to reduce the risk of future occurrences. The plan also includes verifying the effectiveness of these actions, documenting the process, and ensuring continuous monitoring for improvement.
CAPA Review Board = A group that is responsible for overseeing the CAPA process
The board ensures that identified issues are appropriately investigated, root causes are thoroughly analysed, and corrective and preventive actions are effectively implemented.
Risk Assessment = The process of identifying and analysing the impact of potential issues
In the context of CAPA, risk assessment helps determine the severity and likelihood of an issue reoccurring, allowing companies to implement appropriate actions to mitigate or control these risks. It plays a critical role in ensuring that corrective and preventive measures are effective and proportionate to the identified risks.
Correction = Action to fix a nonconformity without addressing the root issue
Unlike corrective actions, which are aimed at preventing recurrence, corrections focus on resolving the current issue.
Preventative Action (PA) = Actions that address the causes of a potential nonconformity
This process involves analysing trends, risks, or weak points in the system and making improvements to avoid future problems, ensuring ongoing compliance and quality.
Corrective Action (CA) = Actions that address the causes of an existing nonconformity
This process involves investigating the issue, implementing changes to eliminate the cause, and ensuring that similar issues do not arise in the future.
Verification = Checking that a solution works as intended
Verification is the process of confirming that a product, process, or system meets specific requirements and functions as intended. It involves checking and testing against predetermined criteria to ensure accuracy and compliance before implementation or release.
Validation = Ensuring that a product or a process meets its intended use
Validation ensures that a product, process, or system consistently meets its intended purpose and regulatory requirements. It involves testing and documentation to confirm reliability and compliance with standards, ensuring product quality and safety.
Effectiveness Check (VoE) = Evaluation to confirm the success of a CAPA
After implementing corrective actions, an Effectiveness Check ensures that the changes have successfully resolved the problem and that the same issue does not reoccur. This check typically involves monitoring the results over a set period, reviewing data, and evaluating the impact of the actions on product quality, performance, or process improvements.
Disposition = Decision on how to handle a nonconforming product or situation
Disposition refers to the decision made regarding nonconforming products, determining whether they should be reworked, used as-is, scrapped, or returned to the supplier. These decisions are based on the severity of the nonconformity and are crucial for maintaining product quality and compliance.
Mastering CAPA: Turning Terminology into Action
In conclusion, understanding and navigating CAPA terminology is essential for ensuring compliance and driving continuous improvement within a quality management system. Familiarity with key terms such as root cause analysis, corrective actions, preventive actions, and effectiveness checks will help professionals make informed decisions, streamline processes, and avoid common pitfalls.
By staying up-to-date with these critical terms, organisations can strengthen their CAPA processes, improve product quality, and enhance overall regulatory compliance. Empowering teams with the knowledge of CAPA terminology is a key step toward maintaining high-quality standards and ensuring the safety and efficacy of medical devices in the marketplace.
Ready to navigate the regulatory process with confidence? With our expert team and 100% notified body approval, we’re here to help you ensure compliance and streamline your medical device journey. Contact us today to get started!